The Use of Flow Rack as an Effort to Implement Kaizen in an Effort to Increase the Production of Stepwagon Car Seats at PT YSC Japan
DOI:
https://doi.org/10.21831/jamat.v1i1.833Keywords:
Kaizen, Efficiency, 8-Step Improvement, Loss Time, Flow RackAbstract
This study aims to: (1) analyze the performance data of workers at PT. YSC Japan before the implementation of an innovation involving the addition of a Flow Rack; (2) examine the process of adding the Flow Rack and its impact on worker performance at PT. YSC Japan; and (3) evaluate how the Flow Rack innovation enhances worker productivity at PT. YSC Japan. The study employs the Kaizen concept using the 8-Step Improvement method, with a fishbone diagram utilized for cause-and-effect analysis. Data were collected through observation and documentation, using instruments such as a logbook, observation sheet, and smartphone. Descriptive quantitative analysis was conducted to compare production speeds before and after process improvements. The findings reveal that: (1) PT. YSC Japan required efficiency enhancements, as production on the Line Front Cushion Stepwagon experienced a loss time of 90 seconds per 22 pieces, resulting in a production time of 38.7 seconds per piece; (2) the application of the Kaizen concept, using the 8-Step Improvement method, successfully improved productivity through the addition of a Flow Rack as a storage innovation; and (3) after implementing this change, PT. YSC Japan achieved a 10.3% efficiency improvement, reducing production time to 34.7 seconds per piece.
Downloads
References
[1] B. Saberi, "The role of the automobile industry in the economy of developed countries," Int. Robotics & Automation J., vol. 4, no. 3, pp. 179–180, 2018. [Online]. Available: https://www.automationjournal.org/content/4/3/179.
[2] Badan Pusat Statistik (BPS), Statistik Transportasi Darat Indonesia 2022, BPS Indonesia, 2024. [Online]. Available: https://www.bps.go.id/publication.
[3] A. Prakoso and R. Putra, Strategi Bisnis untuk Daya Saing Perusahaan, Penerbit Andi, 2021.
[4] T. Dharsono, Dampak Peningkatan Produksi terhadap Efisiensi Kerja, Penerbit Erlangga, 2021.
[5] C. Suwondo, "Penerapan budaya kerja unggulan 5S (Seiri, Seiton, Seiso, Seiketsu, dan Shitsuke) di Indonesia," J. Magister Manajemen, vol. 1, no. 1, pp. 29–48, 2012. [Online]. Available: https://www.jmm-journal.com/volume-1/issue-1.
[6] G. S. Jadhav, V. M. Jamadar, P. S. Gunavant, and S. S. Gajghate, "Role of Kaizens to Improve Productivity: A Case Study," Appl. Mech. Mater., vol. 592–594, pp. 2689–2693, 2014. doi: 10.4028/www.scientific.net/amm.592-594.2689.
[7] W. de Almeida, G. E. O. Giacaglia, W. de Q. Lamas, and F. F. Bargos, "KAIZEN TOOLS FOR PRODUCTIVITY IMPROVEMENT: A Real Case," Eng. Res. Tech. Rep., vol. 6, no. 4, Art. 1, 2016. doi: 10.32426/engresv6n4-001.
[8] T. U. Hoang, "Kaizen Practices Implementation and Operational Performance: An Empirical Study on Manufacturing Companies in Vietnam," Master's thesis, Graduate School of International Social Science, Yokohama National University, Yokohama, Japan, 2017. [Online]. Available: https://www.nationaluniversity.edu/theses/hoang.
[9] A. Dahiya, S. Kadyan, and R. Giri, "Kaizen and 5S: Productivity Improvement Tools for Automotive Assembly Line," NOLEGEIN-J. Oper. Res. Manag., vol. 5, no. 1, 2022. doi: 10.37591/njorm.v5i1.885.
[10] H. Darmawan, S. Hasibuan, and H. H. Purba, "Application of Kaizen concept with 8 steps PDCA to reduce in-line defect at pasting process: A case study in automotive battery," Int. J. Adv. Sci. Res. Eng., vol. 4, no. 8, pp. 97–104, 2018. doi: 10.31695/IJASRE.2018.32800.
[11] A. Fathurohman, "Kaizen Dalam Meningkatkan Efisiensi dan Kualitas Produk pada Bagian Banbury PT Bridgestone Tire Indonesia," 2016. [Online]. Available: https://www.researchgate.net/publication/kaizen-banbury-bridgestone.
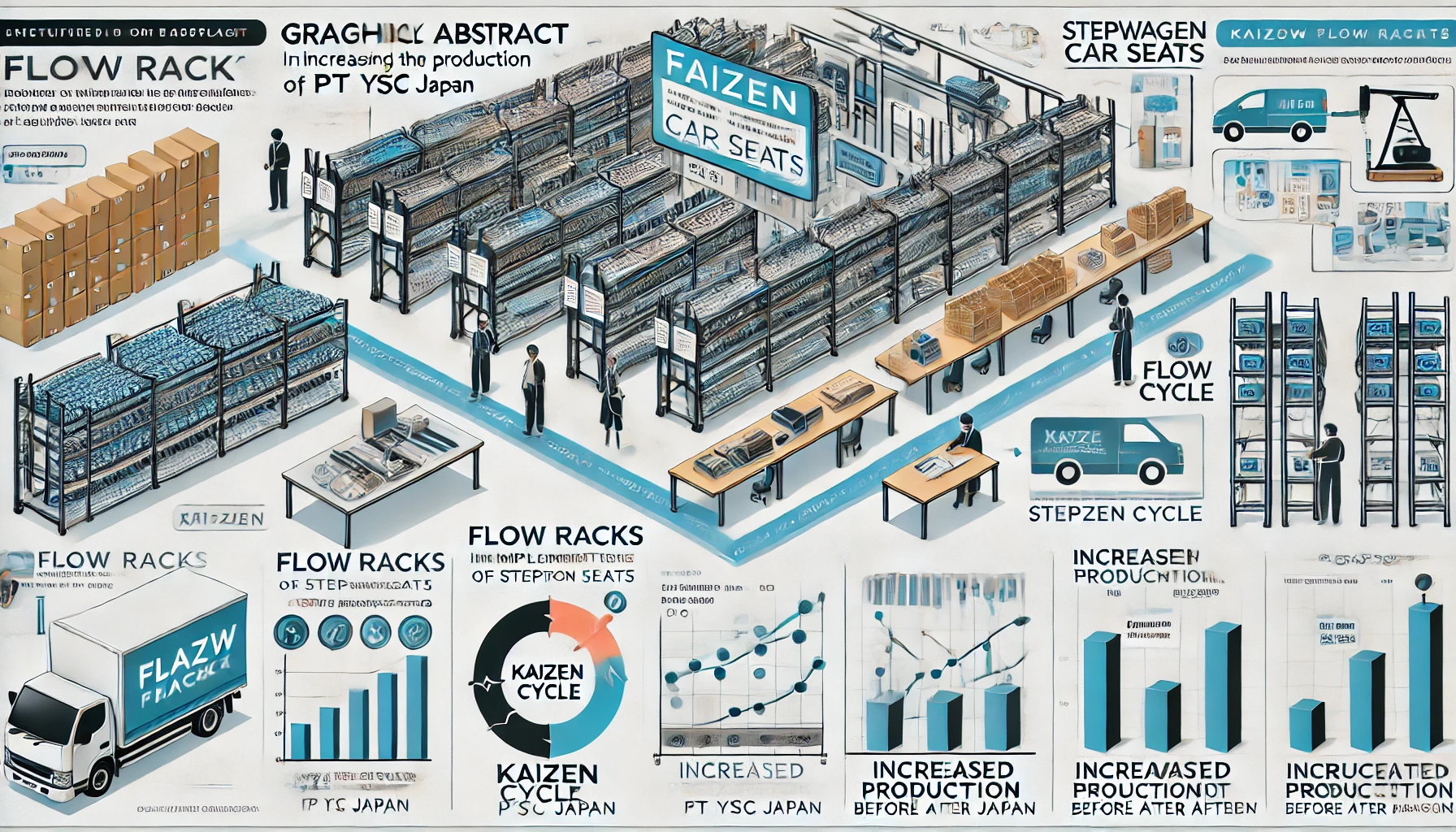
Downloads
Published
How to Cite
Issue
Section
License
Copyright (c) 2024 Journal of Automotive and Mechanical Applied Technology

This work is licensed under a Creative Commons Attribution 4.0 International License.