Design and Analysis of Orbital Pipe Welding Prototype for Piping System Welding Applications
DOI:
https://doi.org/10.21831/jamat.v1i1.797Keywords:
Factor of safety, Orbital pipe welding, Piping system, PrototypeAbstract
Welding the joints of pipes is often required for maintenance and repairs in industrial applications, where pipes are frequently used. A prototype of an orbital pipe welding machine was constructed, and its design, analysis, and construction were carried out. The goal of this endeavor was to improve the quality of the welding process as well as overall productivity. The design study was carried out with the assistance of the SolidWorks program, which allowed for the determination of the stress, strain, displacement, and factor of safety imposed on the gear section throughout the welding and pipe installation process. During pipe installation, the gear section experiences maximum stresses of 3.920e+12 MPa, 5.029e+05 MPa, and 2.239e+06 MPa, respectively. These stresses are a result of the pipe being installed. When the pipe is installed, the highest strain in the gear section is 1.802e+01%, 3.030e-06%, and 8.439e-06%, respectively. This strain happens when the pipe is installed. In addition, the maximum displacement in the gear section is 3.074e+09 mm, 3.215e+04 mm, and 6.312e-03 mm, respectively, when the pipe is mounted and the pipe is installed. With a value of 1.5, the analysis results demonstrated that the maximum stresses, strains, and displacements in the gear section during the welding process are sufficient to fulfill the requirements for the critical safety factor. This demonstrates that the orbital pipe welding equipment may be utilized to generate welds of superior quality while simultaneously enhancing both productivity and efficiency through its utilization.
Downloads
References
References
[1] N. K. Jha, "Design and Analysis of Welding Fixture for Elementary Weld Joints," CVR Journal of Science and Technology, vol. 15, pp. 90-95, 2018, doi: 10.32377/CVRJST1516.
[2] C.-H. Tsai, K.-H. Hou, and H.-T. Chuang, "Fuzzy control of pulsed GTA welds by using real-time root bead image feedback," Journal of Materials Processing Technology, vol. 176, no. 1-3, pp. 158-167, 2006, doi: https://doi.org/10.1016/j.jmatprotec.2006.02.027.
[3] I. Sattari-Far and Y. Javadi, "Influence of welding sequence on welding distortions in pipes," International Journal of Pressure Vessels and Piping, vol. 85, no. 4, pp. 265-274, 2008, doi: https://doi.org/10.1016/j.ijpvp.2007.07.003.
[4] I. D. Harris, "Welding advances in tube and pipe applications," Welding journal, vol. 90, no. 6, pp. 58-63, 2011.
[5] S. K. Sharma and S. Maheshwari, "A review on welding of high strength oil and gas pipeline steels," Journal of Natural Gas Science and Engineering, vol. 38, pp. 203-217, 2017, doi: https://doi.org/10.1016/j.jngse.2016.12.039.
[6] R. Z. Ríos-Mercado and C. Borraz-Sánchez, "Optimization problems in natural gas transportation systems: A state-of-the-art review," Applied Energy, vol. 147, pp. 536-555, 2015, doi: https://doi.org/10.1016/j.apenergy.2015.03.017.
[7] D. Yapp and S. A. Blackman, "Recent developments in high productivity pipeline welding," Journal of the Brazilian Society of Mechanical Sciences and Engineering, vol. 26, pp. 89-97, 2004, doi: 10.1590/S1678-58782004000100015.
[8] Z. Chen, Z. Chen, and R. A. Shenoi, "Influence of welding sequence on welding deformation and residual stress of a stiffened plate structure," Ocean Engineering, vol. 106, pp. 271-280, 2015, doi: https://doi.org/10.1016/j.oceaneng.2015.07.013.
[9] H. Huang, Z. Yuan, H. Qian, Y. Ye, J. Leng, and Y. Wei, "Design and analysis of a novel ship pipeline welding auxiliary device," Ocean Engineering, vol. 123, pp. 55-64, 2016, doi: https://doi.org/10.1016/j.oceaneng.2016.06.050.
[10] M. Bahrami-Samani, M. Agahi, S. Ali, and A. Moosavian, "Design and analysis of a welding robot," 2006 2006: IEEE, pp. 454-459, doi: 10.1109/COASE.2006.326924.
[11] M. M. Ghazaly, S. N. M. Basar, and M. S. Lagani, "Design Optimization & Analysis of a Soft Crawling Robot," International Journal of Integrated Engineering, vol. 13, no. 6, pp. 285-298, 2021, doi: 10.30880/ijie.2021.13.06.025.
[12] A. R. Abd Hamid and T. Jagan, "Design and analysis of carbon fibre composite monorack arm for motorcycle," International Journal of Integrated Engineering, vol. 11, no. 7, pp. 152-161, 2019, doi: 10.30880/ijie.2019.11.07.020.
[13] M. P. Groover, Fundamentals of modern manufacturing: materials, processes, and systems. John Wiley & Sons, 2020.
[14] Y. Ren and R. Skilton, "A review of pipe cutting, welding, and NDE technologies for use in fusion devices," Fusion Engineering and Design, vol. 202, p. 114396, 2024, doi: https://doi.org/10.1016/j.fusengdes.2024.114396.
[15] R. Owsiński, D. S. Lachowicz, C. T. Lachowicz, R. Gil, and A. Niesłony, "Characterisation of joint properties through spatial mapping of cracks in fatigue specimens, extracted from the linearly friction welded steel coupon," Precision Engineering, vol. 71, pp. 78-89, 2021, doi: https://doi.org/10.1016/j.precisioneng.2021.02.008.
[16] P. Horajski, L. Bohdal, L. Kukielka, R. Patyk, P. Kaldunski, and S. Legutko, "Advanced Structural and Technological Method of Reducing Distortion in Thin-Walled Welded Structures," Materials, vol. 14, no. 3, p. 504, 2021, doi: https://doi.org/10.3390/ma14030504.
[17] T. J. Ross, "An enhanced reliability index for assessing margin of safety in structures," in Reliability and Optimization of Structural Systems: CRC Press, 2020, pp. 291-298.
[18] E. Prasetyo, A. S. Baskoro, and A. Widyianto, "IDENTIFYING THE INFLUENCE OF ORBITAL PIPE WELDING PARAMETERS ON MECHANICAL PROPERTIES USING SS316L PIPE," Eastern-European Journal of Enterprise Technologies, vol. 125, no. 12, 2023, doi: 10.15587/1729-4061.2023.287397.
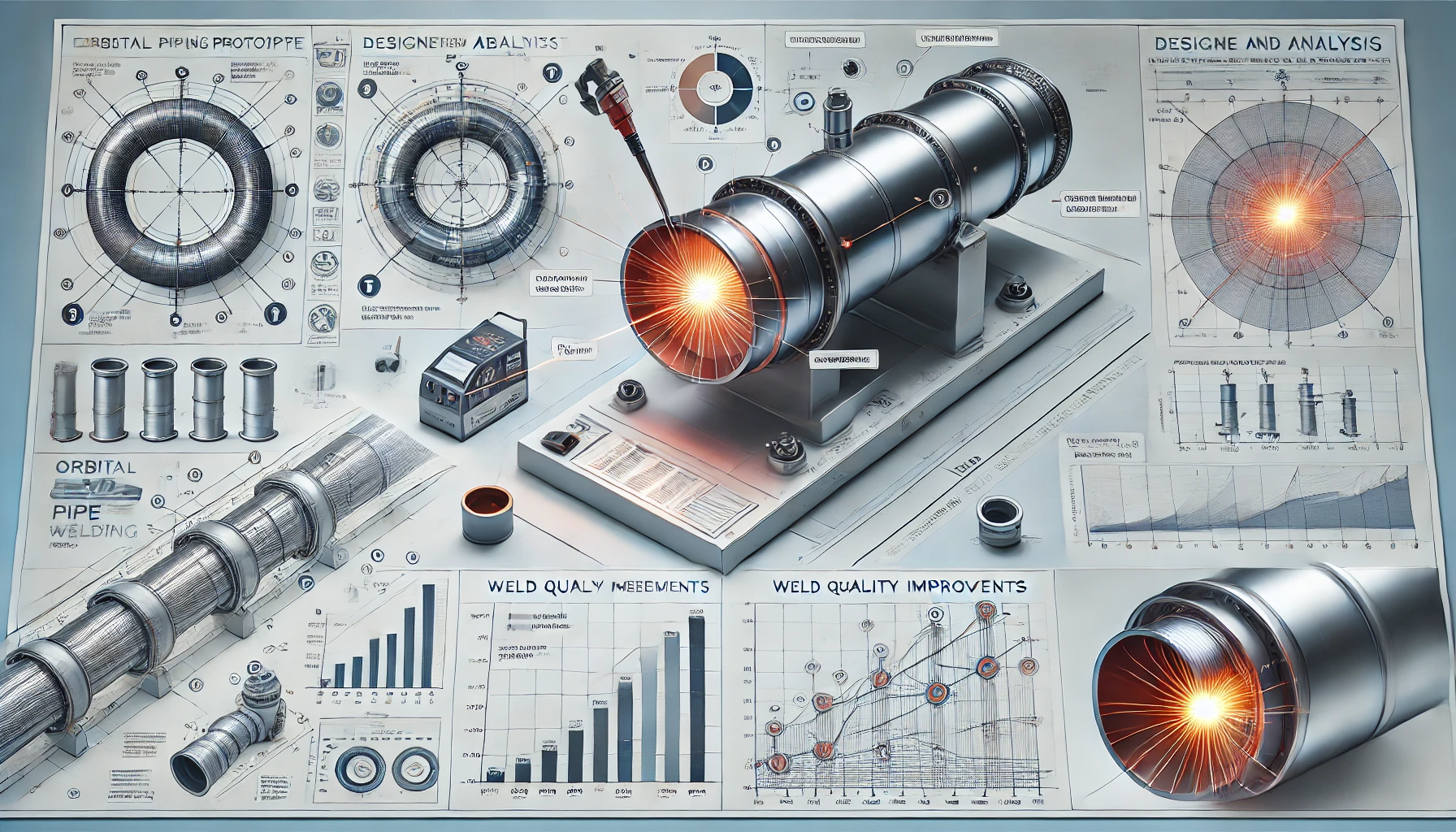
Downloads
Published
How to Cite
Issue
Section
License
Copyright (c) 2024 Journal of Automotive and Mechanical Applied Technology

This work is licensed under a Creative Commons Attribution 4.0 International License.