Experimental study: coolant viscosity’s impact on Inconel 600’s surface roughness measured using a refractometer
Nurman Pamungkas, Department of Mechanical Engineering, Politeknik Negeri Batam, Indonesia
Meilani Mandalena Manurung, Department of Mechanical Engineering, Politeknik Negeri Batam, Indonesia
Ninda Hardina Batubara, Department of Mechanical Engineering, Politeknik Negeri Batam, Indonesia
Hanifah Widiastuti, Department of Mechanical Engineering, Politeknik Negeri Batam, Indonesia
Abstract
This paper presents an experimental study on the impact of coolant viscosity on the surface roughness of Inconel 600 material processed using a lathe. This research employs sequential experimental methods, encompassing a coolant viscosity test, specimen machining with a lathe, and surface roughness test. The standard for the roughness grade number is defined by ISO 1302. The study effectively demonstrates the use of a refractometer as a reliable and practical alternative for determining coolant quality in % Brix units, which strongly correlates with coolant viscosity. The research findings reveal that an increase in coolant viscosity results in a smoother surface roughness of the workpiece, while a decrease leads to an increase in surface roughness. Specifically, the average viscosity of 8%, 10%, and 13% Brix coolant results in an average surface roughness of Ra 11.83 μm, Ra 10.09 μm, and Ra 7.23 μm, respectively. The average roughness grade number based on this study is N9 - N10. However, the study also identifies the need for further mathematical calculations to establish a link between coolant concentration, % Brix, and coolant viscosity. This opens up an intriguing avenue for future research and holds the potential to significantly enhance our understanding of the relationship between these variables.
Keywords
Full Text:
PDFReferences
B. Ghiban, C. F. Elefterie, C. Guragata, and D. Bran, “Requirements of Inconel 718 alloy for aeronautical applications,” In AIP Conference Proceedings, vol. Vol. 1932 No 1, no. AIP Publishing, Feb. 2018.
S. Qadri, G. Harmain, and M. Wani, “Influence of Tool Tip Temperature on Crater Wear of Ceramic Inserts During Turning Process of Inconel-718 at Varying Hardness,” Tribol. Ind, vol. 42, pp. 310–326, 2020, doi: DOI: 10.24874/ti.776.10.19.05.
H. Nomoto, Development in materials for ultra-supercritical and advanced ultra-supercritical steam turbines. In Advances in Steam Turbines for Modern Power Plants, 2nd ed. UK: Woodhead Publishing: Sawston, 2022.
M. E. Kassner, Creep Fracture. In Fundamentals of Creep in Metals and Alloys, 3rd ed. Boston: Butterworth-Heinemann: , 2015.
M. F. Ashby, “Materials Selection in Mechanical Design,” Elsevier Science: Amsterdão, Paises Baixos, 2006.
Lin Liu, Taiwen Huang, Min Qu, Gang Liu, Hengzhi Fu, and Jun Zhang, “High thermal gradient directional solidification and its application in the processing of nickel-based superalloys,” J Mater Process Technol, vol. 210, no. 1, pp. 159–165, Jan. 2010.
J. H. Weber and M. K. Banerjee, “Nickel and Nickel Alloys: An Overview. In Reference Module in Materials Science and Materials Engineering,” Elsevier: Amsterdam, The Netherlands, 2019.
M. E. Kassner, Nickel-Based Superalloys. In Fundamentals of Creep in Metals and Alloys, 3rd ed. Boston: Butterworth-Heinemann, 2015.
H. Dai et al., “Effects of elemental composition and microstructure inhomogeneity on the corrosion behavior of nickel-based alloys in hydrofluoric acid solution,” Corros Sci, vol. 176, no. 108917, Nov. 2020.
D. Deng, Additively Manufactured Inconel 718: Microstructures and Mechanical Properties. Licentiate Thesis, Comprehensive Summary. Linköping, Sweden: Linköping University Electronic Press, 2018.
K. Vinod, Udaya Ravi, and N. Yuvaraja, “A Study of Surface Morphology and Wear Rate Prediction of Coated Inconel 600, 625 and 718 Specimens,” Int. J. Sci. Acad. Res. (IJSAR), vol. 3, pp. 1–9, 2023.
M. Dhananchezian, “Influence of variation in cutting velocity on temperature, surface finish, chip form and insert after dry turning Inconel 600 with TiAlN carbide insert,” Material Today: Proceeding, vol. 46, pp. 8271–8274, 2021.
S. B. Ruggayah, “Analisa Pengaruh Cairan Pendingin Terhadap Tingkat Kekasaran Permukaan Pada Proses Pembubutan Baja ST 42,” Makassar: Universitas Negri Makassar: unpublished, 2020.
G. W. A. Wong, S. Islam, M. M. Reddy, N. Khandoker, and V. L. C. Chen, “Recent progress and evolution of coolant usages in conventional machining methods: a comprehensive review,” The International Journal of Advanced Manufacturing Technology, vol. 119, no. 1–2, pp. 3–40, 2022.
K. A. Alharbi and T. Alotaibi, “THE INFLUENCE OF COOLANT TYPES ON SURFACE ROUGHNESS IN THE TURNING PROCESS,” The American Journal of Interdisciplinary Innovations and Research, vol. 04, pp. 93–112, Nov. 2022.
M. Mia and N. R. Dhar, “Optimization of surface roughness and cutting temperature in high-pressure coolant-assisted hard turning using Taguchi method. ,” Int J Adv Manuf Technol, vol. 88, pp. 739–753, 2017.
P. Sivadasan, G. S., Sharma, I. S. Rout, and P. Pal Pandian, “A Review on Influence of Cutting Fluid on Improving the Machinability of Inconel 718,” Springer Proceedings in Materials, vol. 8, 2020.
L. Y. Beaulieu, E. R. Logan, K. L. Gering, and J. R. Dahn, “An automated system for performing continuous viscosity versus temperature measurements of fluids using an Ostwald viscometer,” Review of Scientific Instruments, vol. 88, no. (9), pp. 95–101, 2017.
Anton Paar GmbH., “Viscosity of Metalworking Fluids in Cutting Processes Determined with SVMTM 3001 or SVMTM 4001 Viscometer.” Accessed: Jan. 31, 2024. [Online]. Available: https://www.anton-paar.com/corp-en/services-support/document-finder/application-reports/viscosity-of-metalworking-fluids-in-cutting-processes-determined-with-svm-3001-or-svm-4001-viscometer/1
M. Kole and T. K. Dey, “Thermal conductivity and viscosity of Al2O3 nanofluid based on car engine coolant,” J Phys D Appl Phys, vol. 43, no. (31), 315501, 2010.
D. D’Addona and S. Raykar, “Thermal Modeling of Tool Temperature Distribution during High Pressure Coolant Assisted Turning of Inconel 718,” Materials, vol. 12, no. 3, p. 408, Jan. 2019, doi: 10.3390/ma12030408.
M. Kole, T. K. Dey, A. Pratap, and N. S. Saxena, “Experimental Investigation On The Thermal Conductivity And Viscosity Of Engine Coolant Based Alumina Nanofluids,” 2010, pp. 120–124. doi: 10.1063/1.3466537.
H. Contreras-Tello, S.-P. C. O., A. García-Valenzuela, R. Márquez-Islas, and Vázquez-Estrada, “Understanding the performance of Abbe-type refractometers with optically absorbing fluids,” Measurement Science and Technology, , vol. 25, no. 7, 2014.
N. Rohmah, “Analysis of the utilization of refractometer tools to test the quality of cooking oil. ,” SAINSTEK: Jurnal Sains dan Teknologi, , vol. 14, no. (1), pp. 41–45, 2022.
Antylia scientific blog team, “Understanding your lab equipment: How a refractometer works. ,” Cole-Parmer. Accessed: Jan. 31, 2024. [Online]. Available: from https://www.coleparmer.com/blog/2013/09/20/understanding-your-lab-equipment-how-a-refractometer-works/
D. V. Udupa, R. P. Shukla, and M. V. Mantravadi, “A critical angle refractometer for heavy water analysis,” Journal of Optics, vol. 40, no. 3, pp. 107–113, Sep. 2011, doi: 10.1007/s12596-011-0043-z.
J. W. George, “The Usefulness and Limitations of Hand‐held Refractometers in Veterinary Laboratory Medicine: An Historical and Technical Review,” Vet Clin Pathol, vol. 30, no. 4, pp. 201–210, Dec. 2001, doi: 10.1111/j.1939-165X.2001.tb00432.x.
B. R. Heidemann, G. Scherpinski, L. Fabris, M. Muller, J. L. Fabris, and G. Pintaude, “Assessing Viscosity in Hydro-Erosive Grinding Process via Refractometry,” SAE Int J Fuels Lubr, vol. 12, no. 3, pp. 04-12-03–0012, Aug. 2019, doi: 10.4271/04-12-03-0012.
“SPECIAL METALS INCONEL ALLOY 600,” Alloy Digest, vol. 69, no. 4, Apr. 2020, doi: 10.31399/asm.ad.ni0758.
MSDS.com, “Blasocut® 2000 CF.” Accessed: Feb. 05, 2024. [Online]. Available: https://www.blaser.com/fileadmin/user_upload/SDS/DE/Blasocut_2000_CF_DE.pdf
British Standard, “Geometrical Product Specifications (GPS) —Indication of surface texture in technical product documentation,” May 16, 2002
V. Vasu and G. Pradeep Kumar Reddy, “Effect of minimum quantity lubrication with Al2O3 nanoparticles on surface roughness, tool wear and temperature dissipation in machining Inconel 600 alloy,” Proceedings of the Institution of Mechanical Engineers, Part N: Journal of Nanoengineering and Nanosystems, vol. 225, no. 1, pp. 3–16, Mar. 2011, doi: 10.1177/1740349911427520.
Shinde Ranjit and S. A. Sonawane, “Effect of Speed, Feed, Depth of Cut on Vibration and Surface Roughness during Turning Operation,” International Journal of Mechanical and Production Engineering Research and Development, vol. 8, no. 4, pp. 819–826, 2018, doi: 10.24247/ijmperdaug201884.
DOI: https://doi.org/10.21831/jeatech.v5i1.71254
Refbacks
- There are currently no refbacks.
Copyright (c) 2024 Journal of Engineering and Applied Technology

This work is licensed under a Creative Commons Attribution 4.0 International License.
Our journal has been indexed by:

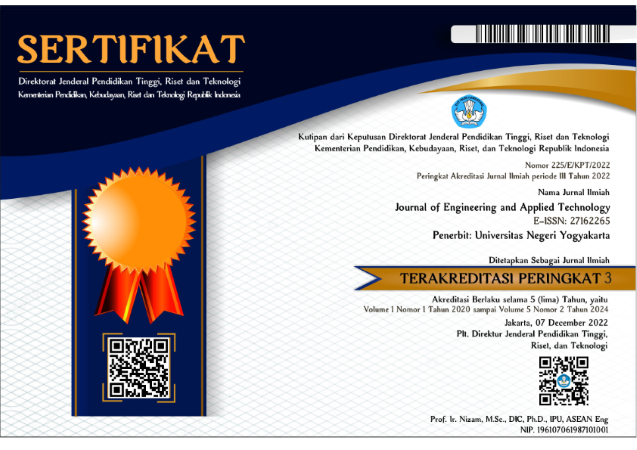
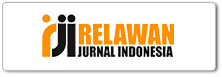
Journal of Engineering and Applied Technology (JEATech) by Faculty of Engineering UNY is licensed under a Creative Commons Attribution-ShareAlike 4.0 International License.